Learn how to use the Kreg K4 Jig for your next home DIY project. This useful tool is a must-have for your toolbox.
This post contains affiliate links for your convenience. For more information, see my disclosures here.
Last year, Ben bought me a DIY book called The HandBuilt Home by Ana White. He knew that I liked home DIY projects and thought it would be a great project inspiration book for our new home. The book is filled with DIY projects where you literally build your own furniture and I love it!
There are all types of project experience levels from beginner to expert, and the book walks you through each project step by step. Since Ben gave me the book, I’ve been flagging my favorite projects and taking notes of what tools I need.
One tool that is used in almost every project is the Kreg Jig. The Kreg Jig is a tool that helps you use your drill to create pocket holes in your project materials. When I first saw that the Kreg Jig was being used in so many projects, I knew I wanted to buy one and have it in our toolbox.
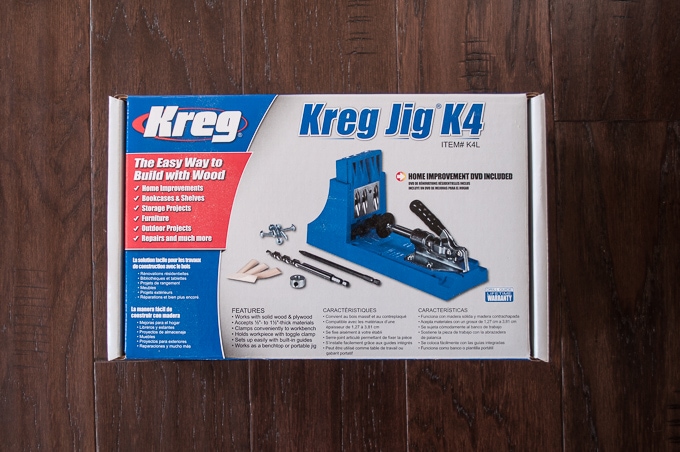
One quick search on Amazon and I realized that the Kreg Jig was JUST a little out of our price range. My first thought was “$100 for a little piece of plastic that helps you drill a hole, there’s no way we are buying that!” But let me tell you, I was totally wrong.
I was putting off buying the Kreg Jig because I didn’t really understand how to use it and I thought it was way to pricey. Ben on the other hand just saw it as “another tool for a job,” and picked it up when he was buying all the materials and tools for our floating shelves project.
I thought it would be great for Ben to take over the blog today and explain all there is to know about the Kreg K4 Jig and why it’s totally worth the investment! Here’s Ben…
The Kreg Pocket Hole Jig is an awesome tool! The ease of use makes it feel very high quality, and it is definitely worth the money that it costs. Having said that, before we bought one, $100 seemed like a lot of money for a tool that didn’t appear to be easy to use. When we finally did purchase the Kreg K4 and used it for our first project, we could not have been more wrong!
Today I am going to teach you how to set up and use the Kreg K4 Jig, and hopefully, take some of the mystery out of this very useful tool.
What is a Pocket Hole? – Why should I Use a Pocket Hole?
The basic concept of a pocket hole is that it allows you to hide your screws on the inside of your project so that no fasteners are visible at the end. Additionally, a pocket hole joint is stronger because the screw threads are holding onto the side of a board, not the end of a board.
The grain inside of wood is actually made up of long strands running the length of the board. To visualize this, imagine a box of spaghetti packed full. If you were to put a screw into the side of this box, the threads of the screw would hold onto the strands of spaghetti and would have to break the spaghetti pieces for you to pull the screw out. Now, imagine putting a screw into the end of the box. Instead of the threads having a secure connection, they would simply push most of the strands aside and sit between them.
This is the strength benefit of a pocket hole, and it is why we decided to use them on the back screws of our floating shelves because that was where most of the weight would be concentrated.
Now that we understand the basic idea of a pocket hole, I’ll show you how to use it and you’ll see why the Kreg K4 Jig is so great!
Step 1: Set your drill bit collar.
The Kreg system ships with a special drill bit and collar to use with the jig. This drill bit is actually two diameters in one. The small section is for drilling a pilot hole for the screw and the larger section is for drilling out enough clearance so that the head of the screw can be hidden inside the wood.
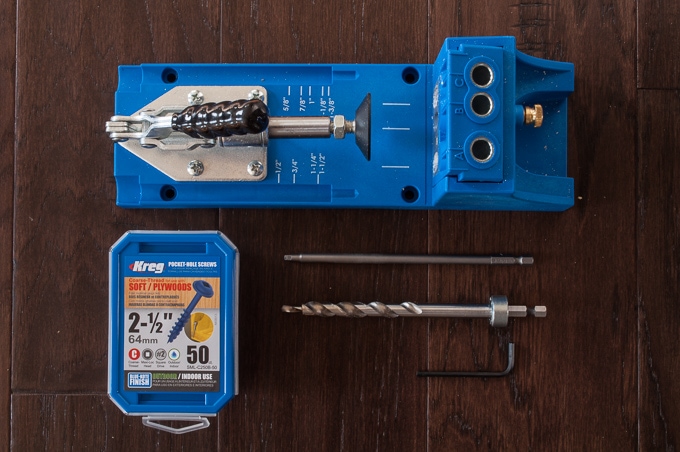
The Kreg drill bit has a collar that slides onto the back of the bit. This collar stops the drill at just the right depth so that you don’t end up drilling too far.
Take the collar and slide it onto the back of the drill bit shaft. The jig has two channels on either side of the clamp with measurement markings that correspond to different board thicknesses. Place your drill bit into the channel with the measurement markings for your specific board thickness.
Slide the drill bit forward until the large section of the drill bit lines up with the measurement mark that you need. For example, a 1.5” thick board would be lined up like the picture below, which is all the way into the channel.
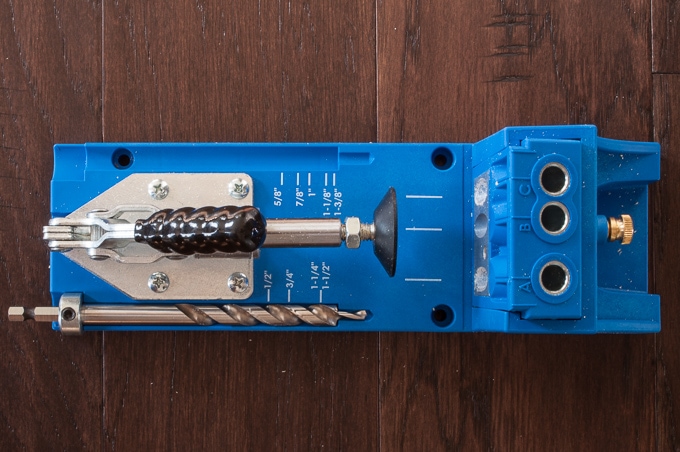
Finally, slide the collar up until it sits properly in the body of the jig and tighten the set screw on the side of the collar using the Allen wrench.
Step 2: Set your hole height.
Now that your drill bit is set to the correct depth, you need to move the angled guide holes up or down. This adjusts where the drill bit will actually enter the wood. The goal here is to have the screw come out right in the center of the board for the strongest joint.
The K4 makes this adjustment really easy because it has markings on the side of the tower piece that correspond to the board thickness. Undo the thumb screw and slide the tower up or down until you find the marking that corresponds to your board thickness. Once you have the measuring mark lined up with the side of the jig, lock the thumb screw into place.
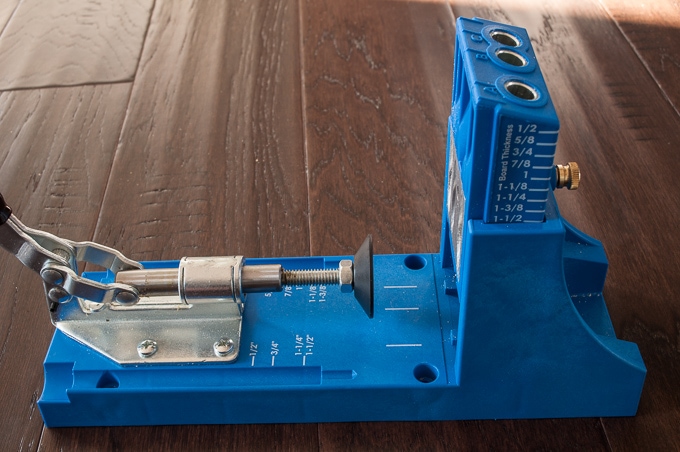
Step 3: Set your clamp distance.
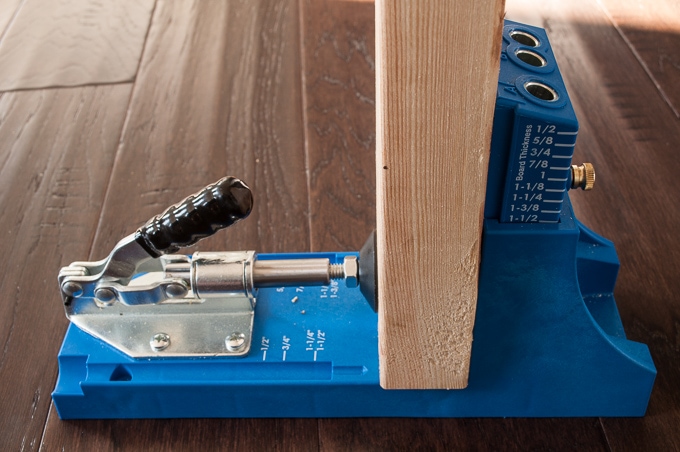
The final step to set up the K4 is to adjust the clamp foot so that it holds onto the board securely. Insert your board into the jig and twist the clamp foot until it comes in contact with the face of the board.
Now, push the lever on the clamp forward to clamp the board in place. If it still feels a bit loose, you can adjust the foot a little to increase the clamping pressure.
Step 4: You are ready to drill!
See the “A”, “B”, and “C” holes on the top of the jig? You will need to use different combinations of these holes depending on the width of your board.
For 1”-2” wide material, use “B” and “C”
For 2”-3” wide material, use “A” and “B”
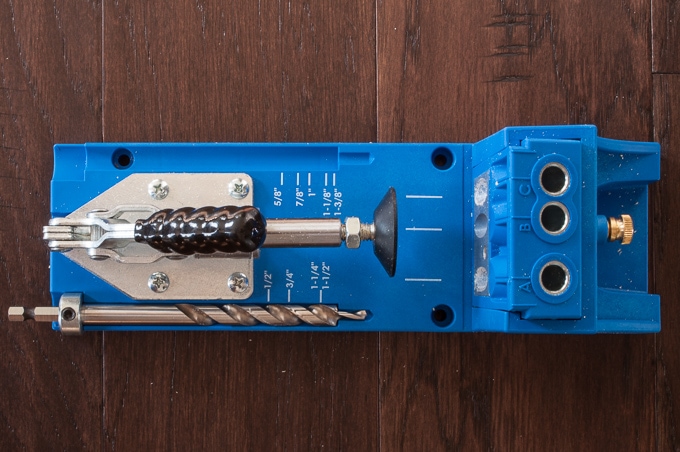
For 3”-4” wide material, use “A” and “C”
As you can see in this mock-up, when the jig is set correctly the drill bit goes almost completely through the board and stops close to the end. The angle is also set so that the screw will come out in the center of the board when making the joint connection.
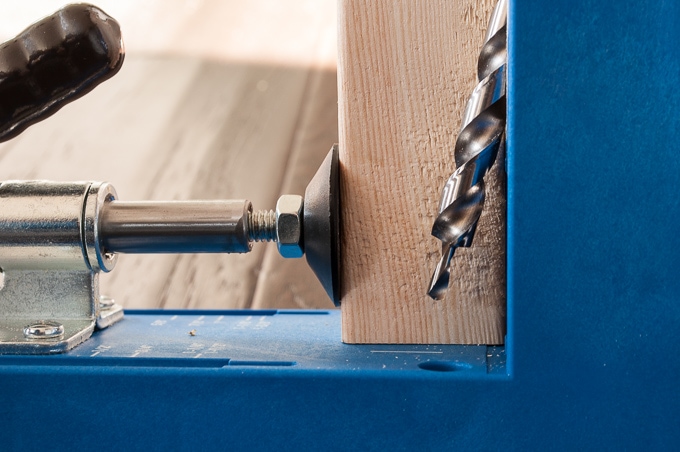
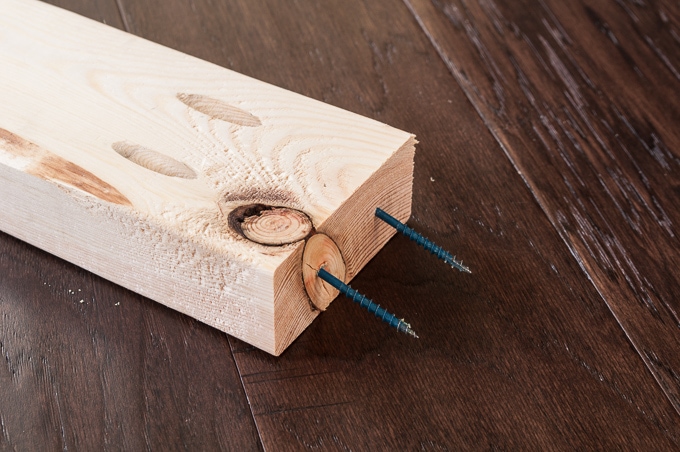
Center and clamp your board across the two holes that you are going to use and insert the drill bit into your drill.
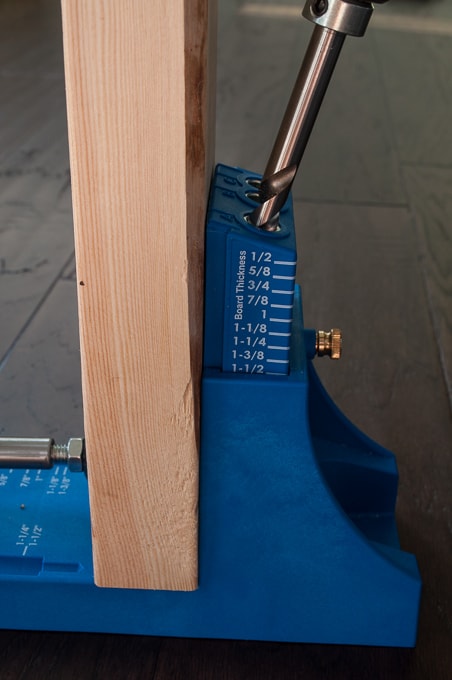
You don’t want to turn the drill on until the drill bit is inside the guide hole because it might jump around a little. With the drill off, insert the bit until it is almost touching the board and then turn the drill on at full speed.
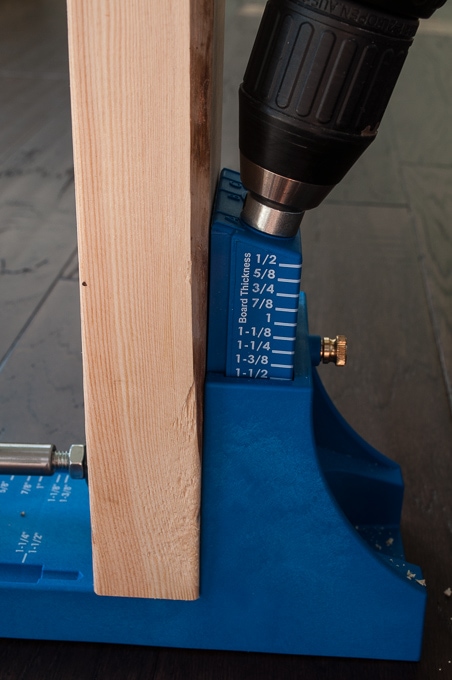
The guide holes will keep everything lined up perfectly and you can drill down into the board until the collar on the drill bit stops you from going any further. If you feel some resistance, you can pull the drill bit out part of the way to release some of the wood chips, and then continue down the full depth.
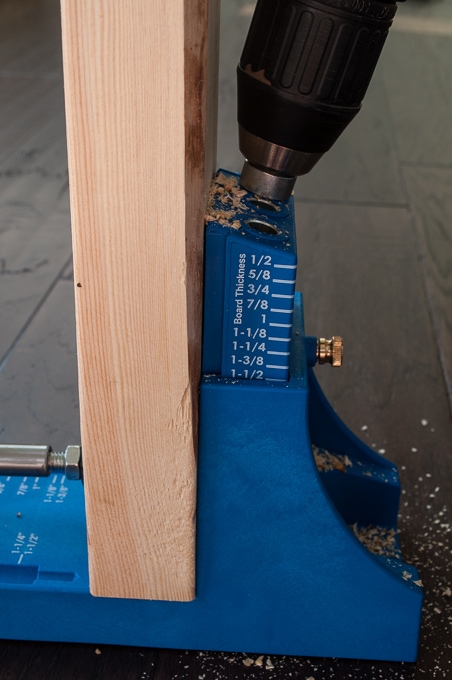
Now, turn the drill off and remove the drill bit from the guide. Repeat this process for your second hole, and unclamp your board.
Step 5: Build your joint.
To assemble your pocket hole joint, you will need the correct length Kreg screws. The Kreg screws are recommended because they include a small drill bit at the tip of each screw that helps the screw secure itself properly.
When purchasing your Kreg screws, look carefully at the recommendations on the back of the screws. The board thickness you are using dictates the length of your screw. When we built our floating shelves we were using 2x4s. The Kreg screw box recommended 2.5” long screws for that type of application. If you plan on using pocket holes a lot in your DIY projects, I would recommend this Kreg screw kit, which includes 675 of the 5 most used screw lengths.
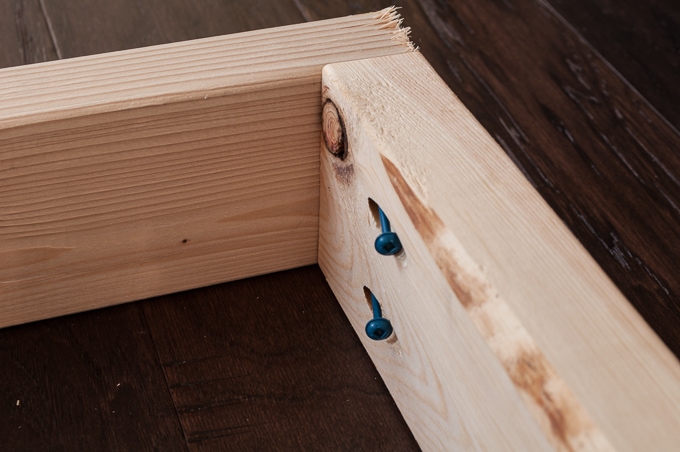
Remove the drill bit from the drill and insert the included square drive bit. The square drive holds onto the screws really well and keeps them from stripping. Insert one screw into each pocket hole.
Clamp or firmly hold the boards together where the joint will be so that they do not move. Then, drive the screw into the pocket hole. Set the torque setting on your drill to around half so that it does not put too much pressure on the joint.
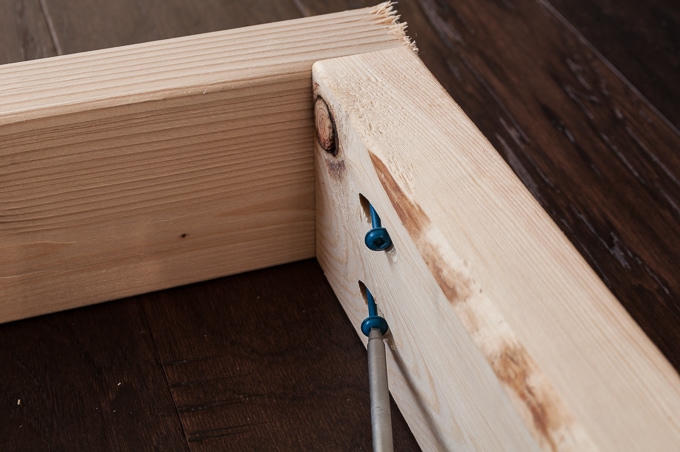
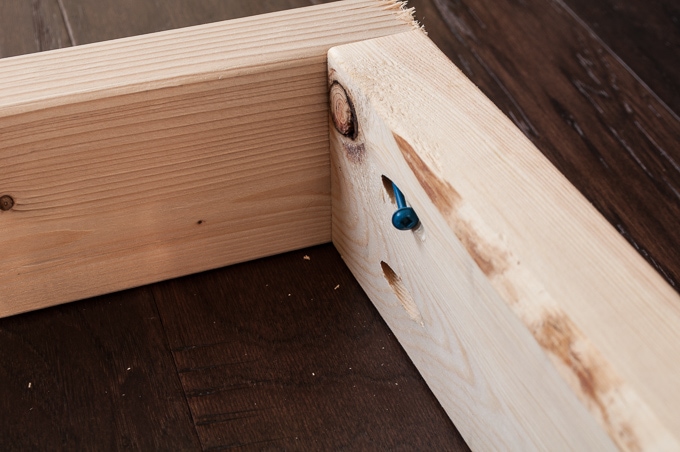
Now you are done! Admire your finished work and new skill!
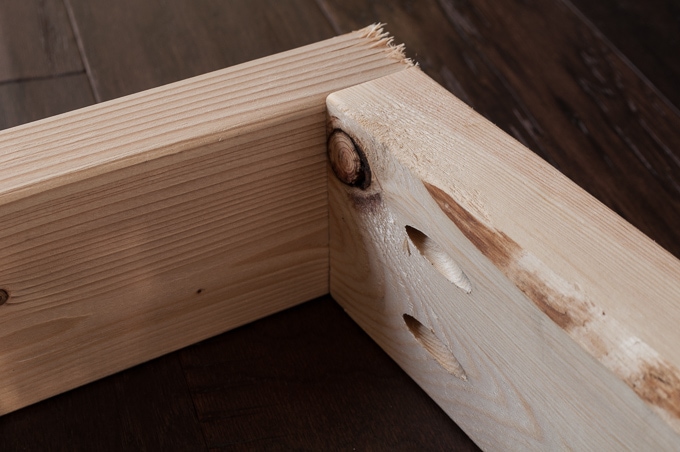
There you have it – 5 easy steps to creating all the pocket holes you will ever need! I hope you were able to follow that quick explanation and see that the Kreg Jig really isn’t that difficult to use. It’s actually an extremely useful thing to have in our toolbox.
Without the K4, there is no way we would be able to line up or drill that type of joint. The Kreg Jig takes all of the measuring guesswork away. All you need to do is line up the pieces with the measurement guidelines and you are good to go.
Pocket holes seem pretty insignificant when you are working on a large project, but they can really make or break the final design. The ability to easily create pocket holes is what makes the Kreg K4 Jig worth the money.
Now that we finally have this tool, I’m back to flagging all the projects in the book that I want to make for our home. I can’t wait to get started! Do you have a Kreg Jig? If not, what’s holding you back from getting one? Also, if you have any other questions about the K4 or how it works, let me know in the comments below. I’ll try my best to answer and if I’m totally stumped, I’ll bring Ben back. 😀
I can’t thank you enough for this crystal clear explanation. This is the most thorough and clear explanation I have found to date. Thank You!
I’m so glad this was helpful Kathryn! 🙂 Good luck on your project!
>> Christene
Thank you so much for this detailed explanation, it is the best I have found! I recently bought a K4 but I still struggle with the correct settings for the drill.
I have one question, when you say that a 1.5” thick board would be lined up like the picture below, which is all the way into the channel, the white mark of 1 1/2 is not “centered” with the wider part of the drill. I don’t know if I make sense… Maybe that’s why my holes don’t hide the screws totally.
I would love any light about this! Thank you in advance!
Hi Pili,
We noticed this too on the K4. For some reason, the marking for 1.5″ does not have its own white line. Instead the 1.25″ and 1.5″ are shown next to the same line. But that line is actually for 1.25.” It’s kind of confusing to look at but to get 1.5″ your drill bit needs to be all the way into that slot (full depth).
Hope this helps – if you have any more questions, feel free to let me know.
>> Christene
Wood that is 1.25″ and 1.5″ thick should both have the collar on the drill bit set to that line. The line is shared because wood 1.5″ thick needs longer screws.
You set your drill up for 1-3/8″. The bit should have been on the 1-1/2″ line. And you should set it where the sharp flute starts. FYI 🙂
Wow! there is so much to read through here. I like your post quite much. And obviously thanks for the detailed description. I found so many new things and information while reading your post.. Just want to give a thumbs up for your great work.
Hi,can you tell me if your using stock that is less than the markings on the kreg jig such as 10mm stock can you not use this size stock.
Also how do you join two different thickness stocks together,no instructions to do this.
kind regards
Chris
how is the best way to connect a mitered corne say 45 degree or less on 1 inch pine. Is this even. possible?